Azobé Wood
Azobé also goes under the name iron wood. One cut through the wood takes between 12-15 minutes. As comparison, a cut through Douglas fir takes approx. 3 minutes. It makes our furniture heavy, weatherproof and incredibly durable.
Azobé wood’s qualities
We work exclusively with reclaimed wood from decommissioned Danish harbours. The wood is called azobé and originates from West Africa. The solid azobé wood is extremely dense and has a high content of natural oil. This makes the wood practically impermeable and resistant to fungus and other typical threats to wood. Our furniture is therefore sturdy, heavy and durable, requiring very little maintenance.
The wood is certified FSC® Recycled 100%.
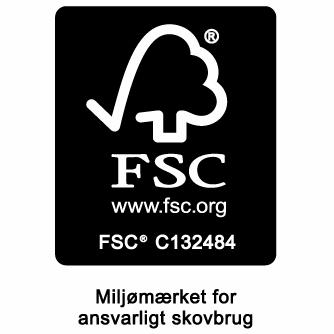
”It was love at first sight when I first saw the wood. From here, it took me several years to develop the technical know-how to cut and control it. However, now we master it, and it was worth all the trouble".
/ Carsten Thor
Durability
Azobé wood is one of the strongest timbers in the world with a hardness og 3220 Janka.
In comparison, oak has a hardness of 730 Janka. This is the reason that azobé wood is used in harbour projects all over Europe. Despite having been partially submerged in the sea, exposed to the harsh elements and withstanding the brutal battering from the many ships docking in the harbour for over 60 years, only the outer layer of the wood bears testament to this. Under less extreme conditions, the wood is considered to be indestructible. Because of this, our furniture can last for generations, whether they are used inside or outside.
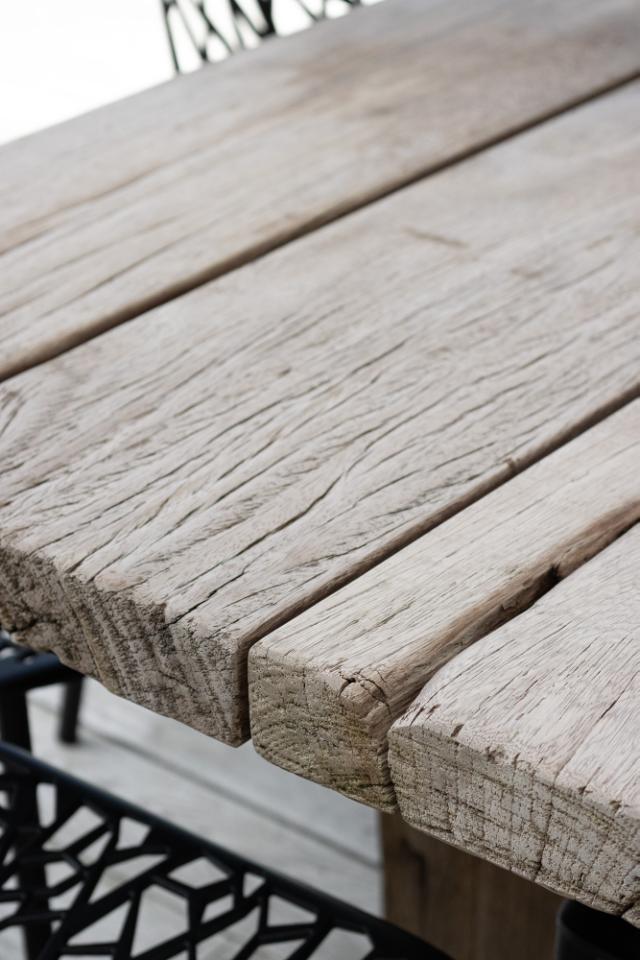
Janka
Janka hardness measures how strong and durable a species of wood is. The higher the Janka value, the more durable the wood.
In practice, the force required to embed an 11.28 millimetre steel ball halfway into a wooden sample is measured.
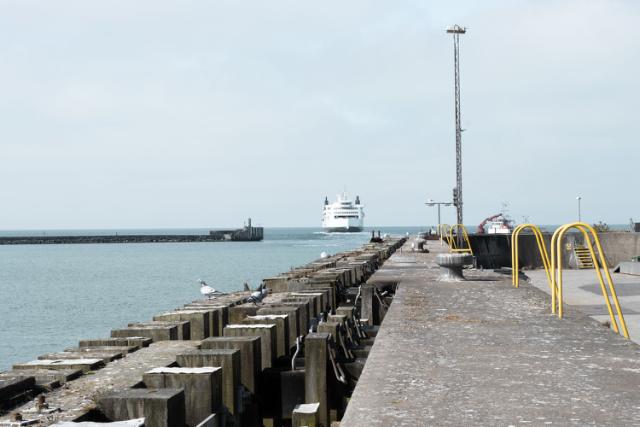
”For me, it is important
that you can see where the wood comes from.
We don’t just sell furniture.
We sell a piece of Danish history”.
/ Carsten Thor
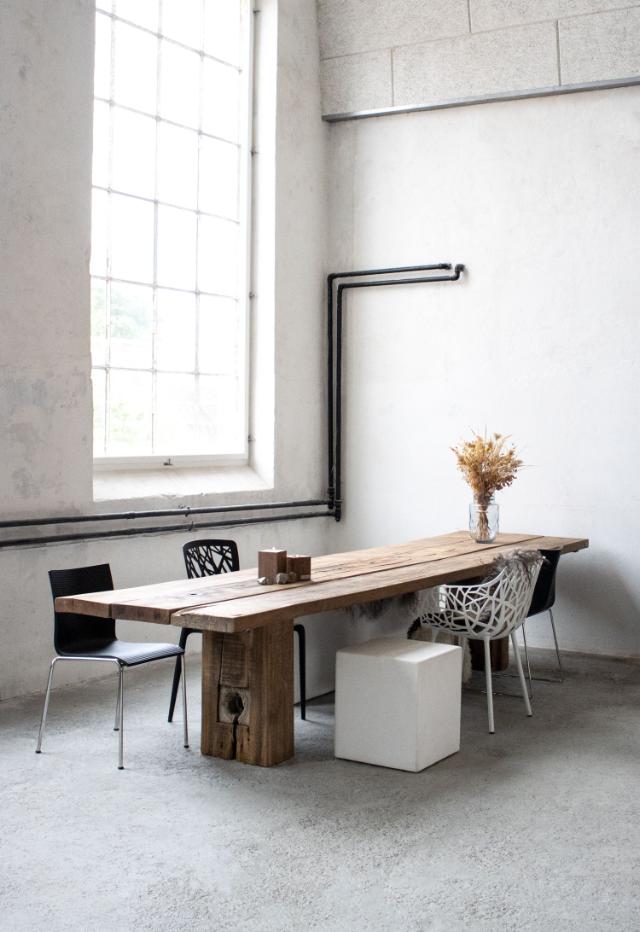
Strength
The density of the wood adds to its extreme strength. We have to use particularly robust brackets to control the powerful planks. We can’t saw the wood in to planks and let them dry out before making them in to pieces of furniture, we have to secure them shortly after the are cut. Therefore, you should expect that your furniture can change and even twist a little over time, as it dries out. Our solid and specially designed brackets almost always hold the wood in place. In seldom cases, the wood can twist so much that the plank has to be changed and we are of course happy to help with this.
N.B. The longer the planks are, the more chance there is, that they may twist.
Marked by the harsh harbour environment
We take great care to treat our wood with the utmost respect for its unique history. All the marks, holes, bolts and other details you see in our furniture are simply a testament to the authenticity of the wood, and can only be preserved because everything is handmade.
Although the wood has been exposed to the harsh elements for more than half a century before being upcycled to furniture, you should expect the woods colour and structure to change further over time. Cracks and crevices can develop as the wood dries.
The most dramatic change in the wood’s colour and structure will occur when the furniture is placed outside. The sun will change the wood to a silver grey colour and changes in the humidity will make the wood constantly expand and contract. If new furniture is exposed to a long period of sun coupled with low humidity, then large cracks can suddenly appear and the wood fibres can rise, creating a rough feel to the surface. The table surface can easily be sanded smooth again.
The constant change in your furniture is to be expected when working with living materials. The way the wood changes adds new details and character to the furniture.
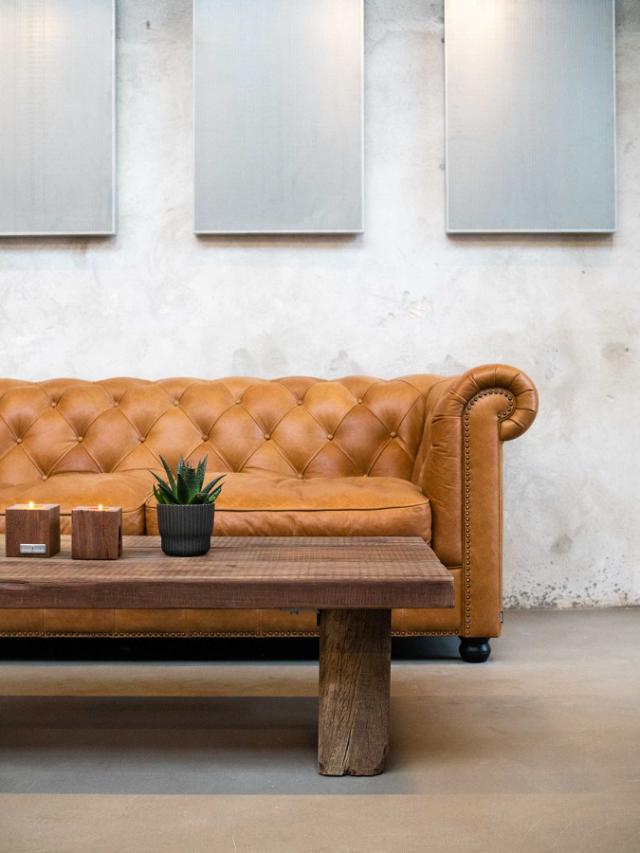